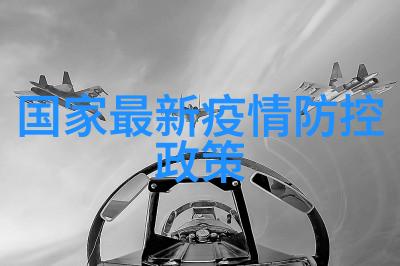
高速注塑模具与普通模具的区别
在现代制造业中,注塑技术作为一种高效、节能的成型方法,其应用范围不断扩大。其中,高速注塑技术因其快速生产速度和高产量特点而备受关注。然而,这种技术背后的关键——高速注塑模具,却与传统的普通模具有本质上的区别。本文将详细探讨这两种模具之间的差异,并分析它们各自适用的场景。
首先,我们来了解一下什么是高速注塑技术及其所需的高速注塑模具。在标准条件下,传统的热压成形过程通常需要数秒至几十秒完成,而高速注塑则可以在1-3秒内完成整个成型过程。这意味着不仅生产速度快,而且产品质量也得到了保证,因为短时间内减少了材料接触温度和时间,从而降低了产生缺陷和变形的可能性。
对于实现这一目的至关重要的是专门设计用于高速操作环境下的硬件设备——即高速注塑机。这种机器能够提供足够大的力矩,以便于在极短时间内进行充分压实材料,使之达到所需形状。此外,由于工作速率非常高,因此必须考虑到冷却系统以确保产品表面光滑且无裂纹。
现在,让我们深入探讨不同类型模具的一些关键区别:
材料选择:由于高速操作要求更强壮耐用,同时保持较好的精度,因此使用特殊合金钢制成,如H13或P20等,以应对巨大的冲击力和摩擦力。此外,还会采用耐磨抗腐蚀性的表面处理,如钝化或镀膜,以提高摩擦系数并防止磨损。
结构设计:为了应对更快、更频繁地开闭周期,结构设计变得更加紧凑且具有优化过的小误差。当相邻部分重叠时,它们被精密铸造或加工为一体,从而减少移动部件数量并简化维护过程。这也意味着所有动态部分都必须经过严格校准以确保最小误差,并能承受巨大的冲击负荷。
精度要求:由于需要快速、高精度地形成复杂三维结构,因此速射模型需要比普通模型要更加精确。这包括边缘尺寸控制、内部孔洞位置以及整体几何轮廓等方面。在这些方面,小错误可能导致整个生产线上延迟甚至失败,所以只能使用具有极高精度标准的手工制作或者CNC(计算机数控)加工工具来创建这些模型。
生产成本:尽管初期投资可能更多,但长远来看,通过提高效率和降低劳动力需求,可以显著减少总体成本。同时,更有效率的运行意味着更少的人员参与,即使是人工检查也是必要但相对较轻松的事务,因为空间利用最大化使得人员密集区域最小化。而对于普通模型,则主要依赖人工操作,这样虽然初期投资较低,但随着规模增长及每小时额外劳动力的需求增加,将逐渐超出起步成本所带来的优势范围之外。
应用领域:不同的行业有不同的需求,其中某些行业如汽车零部件制造商可能会偏好使用普通模型,因为他们经常只生产大量相同部件;而那些涉及多样性、高复杂性产品,如电子设备配件或者医疗器械,则更倾向于采用高度定制化、可重复性高等级测试确认品质可靠性的提升,以及物流管理相关的问题解决方案中的个性化解决方案,有助于避免错误和缩短反馈循环时程从而加速创新进程。
维护与升级能力:由于其结构简单且易于访问,大多数用户认为旧式金属印刷机容易维护。但是,当它们老旧时重新安装新齿轮或其他零部件变得困难时,他们就不再那么“易于”了。而最新款的大型喷墨打印机拥有更开放式框架,这允许用户很容易地替换任何故障发生的地方,无论是在电路板还是机械部件上,都可以轻松替换。
绿色考虑因素: 为了满足日益增长的人口以及全球资源稀缺问题,对环境友好的原则越发受到重视,不同地区法规也越发严格限制工业排放量。因此,在选择适合未来发展趋势的地方,它们正在寻求通过绿色能源解决方案,如太阳能供电系统,与此同时还要注意如何尽量减少废弃物品造成污染的问题,比如回收利用材料做新的原料去掉浪费。
8最后,一些企业发现自己处在一个转型阶段,他们开始将自己的业务模式从传统纸张出版转移到数字出版领域,而这涉及到改变既有的物理空间布局以容纳新的设备并培训员工进行新技能学习这样的重大变化。如果没有正确规划,该转变可能会迅速耗尽资源并导致公司破产。在这种情况下,对待新技术的一种普遍态度就是审慎谨慎,但仍然愿意尝试它,因为这样才能让公司生存下去,并为未来的成功奠定基础。
综上所述,即使功能相似,但基于不同性能需求下的两种类型分别针对不同的应用场景,其经济效果也有根本上的不同。不论哪一种都是现代制造业不可或缺的一个组成部分,每一项都为工业界提供了一定的灵活性,使其能够根据市场变化迅速响应,从而保持竞争优势。